cement clinker grinding costs
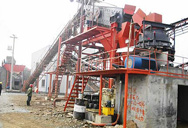
Sustainable transition towards biomass-based cement industry: A
2022年7月1日 The distribution of electricity consumption across critical unit operations is as follows: cement grinding (31–44%), clinker production (28–29%), raw material grinding (26%) and fuel grinding [17].
More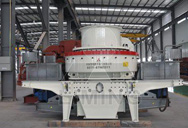
CAPTURING VALUE IN THE U.S. CEMENT INDUSTRY WITH A
A grinding plant can combine imported clinker with less cost sourced materials (e.g., limestone, coal ash, slag, etc.) to make blended / specialty cements at higher profits. The US is quite
More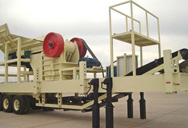
An Introduction to Clinker Grinding and Cement Storage
Clinker Grinding. The cement clinker is ground as finished cement, in a vertical roller mill for cement or in ball mills similar to those normally used for grinding hard raw materials in dry and
More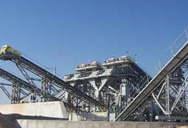
(PDF) A study of different grinding aids for low-energy
2023年10月23日 Cement production requires significant energy, and entails high costs and CO2 emissions. This is because the clinker requires very fine grinding. Grinding aids can improve production and...
More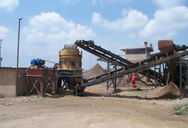
Thermodynamic modelling of cements clinkering process as a tool
2023年10月16日 This study proposes a raw meal proportioning methodology for optimising co-processing of natural feedstocks with alternative raw materials in clinker production, intending
More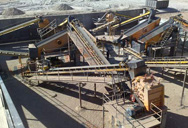
Efficiency enhancement and cost reduction in cement clinker
2024年8月1日 A modern cement plant's electrical energy use was around 110–120 kWh per tonne of cement. The burning process consumes majority of thermal energy, while cement
More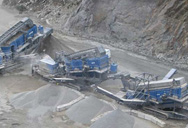
(PDF) Pregrinding technology - ResearchGate
2006年11月1日 Grinding is a high-cost operation consuming approximately 60% of the total electrical energy expenditure in a typical cement plant. There is potential to optimise the
More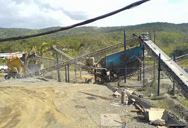
Cement Clinker Production - an overview ScienceDirect Topics
This section provides an in-depth review of major solutions deployed to decarbonize cement manufacturing, including alternative formulations of clinker, alternative fuels for cement
More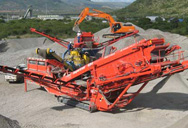
Breakthrough in Clinker Grinding - Massachusetts Institute of
2012年11月8日 Finish grinding of clinker and other cement ingredients reduces 25 mm clinker balls to particle sizes optimally ranging from 3 to 30 microns. The European Cement
More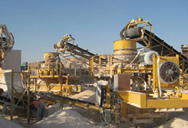
Clinker Grinding Techniques in Cement Manufacturing
2023年10月19日 Explore the significance of clinker grinding in cement manufacturing, from particle size reduction to improved reactivity and quality control. Learn how this integral process transforms clinker into the final
More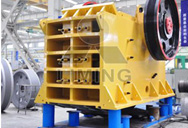
Cement Clinker: Types and Uses of Cement Clinker JK Cement
Discover what is Cement Clinker its vital role in cement production. Explore its formation, ... The formability and short curing time of cement also contribute to the speed and cost-effectiveness of building. ... The rapid cooling process is crucial to achieving the desired properties of the clinker. Grinding.
More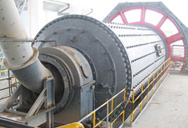
An Introduction to Clinker Grinding and Cement Storage
would be a length of 13.5 m and a diameter of 2.5 m, with a speed of approximately 20 revolutions per minute. Such a mill would normally have a load of approximately 90 tons of grinding media, graduated from 90 mm to 60 mm in the first chamber, 50 mm to 15 mm in the second chamber and 15 mm down in the final chamber.
More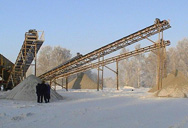
Clinker factors will be pushed downwards - Indian Cement Review
2024年8月23日 New-age quality improvers will replace conventional grinding aids in helping cement producers achieve the desired cement performance with much lower clinker factor. Thirdly, grinding aid suppliers will have to improve their offerings, deliver high impact products, and still ensure cost effectiveness of their products.
More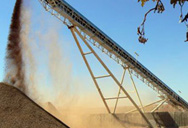
Cutting-Edge Grinding Solutions - Indian Cement Review
2023年8月21日 ICR looks at the inner workings of grinding mills in the cement industry to understand the technological advancements that are reshaping the landscape against the foreground of sustainability. Innovations to enhance the grinding processes are aimed at minimising their environmental footprint while increasing efficiency and performance. In
More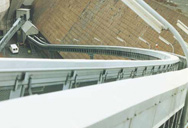
OPTIMIZATION OF CEMENT GRINDING OPERATION IN BALL MILLS
OPTIMIZATION OF CEMENT GRINDING OPERATION IN BALL MILLS Several energy efficient options for cement grinding are available today such as vertical roller mills, roller presses (typically in combination with a ball mill), and clinker pregrinder- s with ball mills. Ball mills have been the traditional method of comminution in the mineral processing
More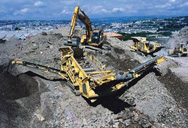
The Comprehensive Guide to Cement Plant Costs: An In-Depth
The Comprehensive Guide to Cement Plant Costs: An In-Depth Look at Equipment, Workforce, and Material Costs. Leave a Comment / HOME / By admin . Previous Post. ... The cement mill grinds the clinker to a fine powder, which is then mixed with gypsum to form cement. Equipment: Ball mills, vertical roller mills.
More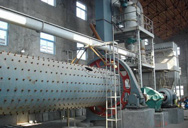
Cement grinding Vertical roller mills VS ball mills
The benefit of the OK mill is in particular pronounced when grinding to a high fineness and/or when slag is included in the cement. Grinding aid For ball mills grinding OPC to a fineness of up to around 3600 cm2/g (Blaine) grinding aid is usually not required; it may not even be feasible considering the cost of grinding aid.
More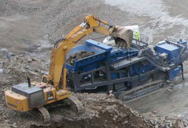
What is Cement Clinker? Composition, Types Uses - Civil
Clinker is a nodular material produced in the kilning stage during the production of cement and is used as the binder in many cement products. The lumps or nodules of clinker are usually of diameter 3-25 mm and dark grey in color. It is produced by heating limestone and clay to the point of liquefaction at about 1400°C-1500°C in the rotary kiln. ...
More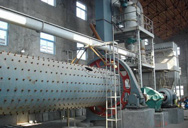
CAPTURING VALUE IN THE U.S. CEMENT INDUSTRY WITH A GRINDING
clinker and grinding is lower than the cost of importing cement, the grinding plants should be profitable for every perceivable shipping cost. ... US$ 24 per metric ton landed cost of cement. If clinker is imported, then several types of cement can be produced from that clinker, ...
More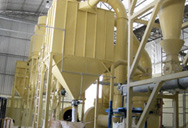
Clinker Grinding Unit - Clinker Grinding Plant Cost - Cement
The clinker grinding unit is a factory specially used to finely grind cement clinker into fine powder to provide basic raw materials for cement production line. Skip to content. ... minimizing transportation costs and meeting demand in densely populated areas.
More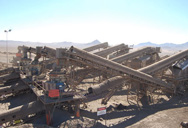
CRUSHING AND GRINDING SEMINAR - The Cement
The purpose of the training is to Identify and understands necessary known and unknown information towards the completed cycle of the crushing and grinding system. Throughout the course the lectures are supplemented with exercises
More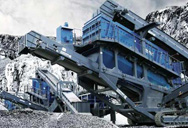
A comprehensive investigation of a grinding unit to reduce
(MC) costs of raw meal are calculated to be 5.05 $/ GJ and 4.13 $/ton, respectively. It is investigated that the hot gas supply to the grinding unit and decreas-ing the moisture rate of feeding materials decreased the SPECO of raw meal, clinker and cement by 8.25%, 5.49% and 4.89% respectively. The applica-
More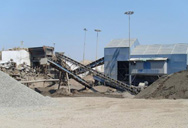
Energy-Efficient Technologies in Cement Grinding
2016年10月5日 1. Introduction. Cement is an energy-intensive industry in which the grinding circuits use more than 60 % of the total electrical energy consumed and account for most of the manufacturing cost [].The requirements for the
More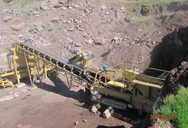
Differences between Clinker Grinding Plant and Cement Plant ...
2023年2月13日 Clinker grinding plants have a simpler production process, lower capital costs, and lower maintenance costs, making them more suitable for small-scale or regional projects. The lower profit margins of clinker grinding plants
More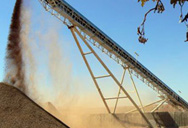
Cutting-Edge Grinding Solutions - Indian Cement Review
2023年8月21日 ICR looks at the inner workings of grinding mills in the cement industry to understand the technological advancements that are reshaping the landscape against the foreground of sustainability. Innovations to enhance the grinding processes are aimed at minimising their environmental footprint while increasing efficiency and performance. In
More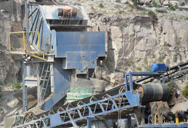
Energy efficiency in clinker production - Indian Cement Review
2017年7月31日 It covers from mill internals to the use of grinding aids. A cement clinker is usually ground using a ... circuits use more than 60 per cent of the total electrical energy consumed and account for most of the manufacturing cost. The requirements for the cement industry in the future are to reduce the use of energy in grinding and the ...
More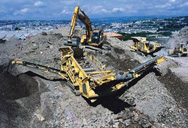
The Comprehensive Guide to Cement Plant Costs: An In-Depth
The Comprehensive Guide to Cement Plant Costs: An In-Depth Look at Equipment, Workforce, and Material Costs. Leave a Comment / HOME / By admin . Previous Post. ... The cement mill grinds the clinker to a fine powder, which is then mixed with gypsum to form cement. Equipment: Ball mills, vertical roller mills.
More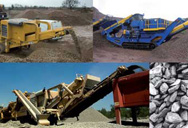
Overview of cement clinker grinding - ResearchGate
2023年1月1日 As a result, grinding y ash with clinker and the use of cement chemicals contribute to the cement sector in terms of sustainability. It is possible to produce cements with improved mechanical ...
More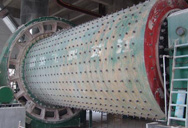
Clinker is the new gold in Kenya - Global Cement
2024年5月8日 Yet, considering how Bamburi Cement argued against the clinker levy, there might have been some commercial thinking here too in order to sell products that use less clinker. Finally, despite completing its divestment of Uganda-based subsidiary Hima Cement for US$84m in March 2024, Bamburi Cement reported a loss of US$2.99m in 2023 compared to
More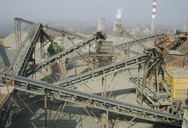
Are you ready to grind? - World Cement
2023年8月14日 Pfeiffer, explains how modular grinding plants can help bring cost-effective, efficient clinker grinding to cement plants around the world. For full functionality of this site it is necessary to enable JavaScript.
More- equipements de transformation de granit en chilee
- concasseur à moteur diesel de vente pour la vente
- atividades no britador
- installation gauche du broyeur à marteaux
- pierre efisiensi concasseur inde
- broyeur à marteaux broyeur de Calcite et la taille des particules
- la pâte d arachide machine de broyage
- concasseur de pierres et tamis
- broyeur et le broyage
- sable siliceuse
- charbon fabricant de la Congo de briquette
- Petit concentrateur centrifuge récupération d'or
- travaux complets de broyeur
- usages des broyeurs de roches et des machines lapidaires
- Concasseur à mâchoires portable 370 tph Jordanie
- Prix concasseur kefid de type PEX 250 1000